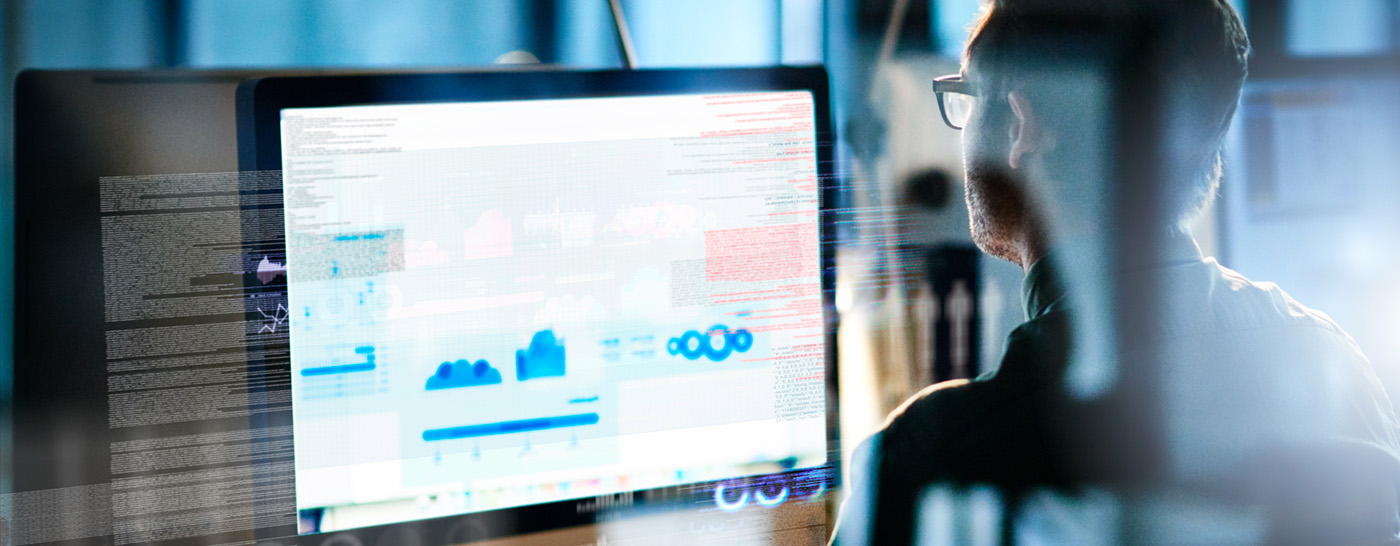
About
Chemical looping reforming is considered one of the most promising technologies for syngas generation with inherent CO2 capture because of higher efficiency than conventional CO2 capture technologies.
The term ‘chemical looping’ is used to describe a reaction that breaks down into individual reactions in which the intermediates – also named oxygen carriers (OCs) – continuously cycle and regenerate. To make the process feasible, the OC should have catalytic properties which can apply to the steam reforming process, as in the case of Nickel materials.
The RECYCLE concept relies on a chemical looping process operated at high pressures in adiabatic packed bed reactors. It consists of three dynamically operated reactors. Each reactor is sequentially exposed to:
The RECYCLE technology can be applied to hydrogen production with flexible design for other syngas-based products that make this process suitable for several energy and carbon-intensive processes such as
Direct Reduction of Iron (steel manufacturing)
Methanol synthesis (alternative transportation fuels such as maritime sector)
Liquid fuels via Fischer-Tropsch for transportation (e.g. aviation)
Ammonia synthesis which is a viable option to reduce the hydrogen storage intensity
Fuel for the RECYCLE process can be fossil fuel-based feedstock such as natural gas, light hydrocarbons and waste streams from refineries or chemical plants such as flare gases. Alternatively, bio-based feedstocks can be integrated such as biogas, bio-waste liquids and other biomass-derived syngas.
The RECYCLE project is partially funded by the Department for Energy Security and Net Zero (DESNZ), and its Net Zero Innovation Portfolio (NZIP).